Linde connect:charger battery charging management avoids energy load peaks
Performance Yes, Load Peaks No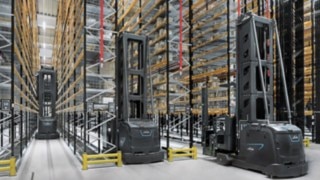
Simply uttering the words ‘load peaks’ is often enough to bring logistics managers out into a cold sweat. After all, these peaks, which occur when multiple lithium-ion batteries are being charged at the same time, can become real cost drivers—unless you have a clever charging management system to hand. The considerable added value that charging management can unlock is impressively demonstrated by the example of Arvato.
Eight years is an eternity in today’s incredibly dynamic tech industry. The intralogistics sector is no exception, with fundamental changes taking place over the same period of time.
Energy is a subject that regularly occupies the minds of logistics experts: “When we started planning our new distribution center in Hamm in 2016, the focus from a logistics perspective was more on the connected load required to charge our very narrow aisle trucks,” recalls Tibor Sevenheck from Arvato’s Future Warehouse team. “It was simply not foreseeable at the time that electricity prices would be such a major cost driver in the long term, but rather the grid fees for this connected load.” However, the cost of energy at the Hamm facility has increased significantly for the logistics and fulfillment service provider in the period from 2016–2024. Sevenheck: “It was clear that we had to take action, without compromising our logistics performance.”
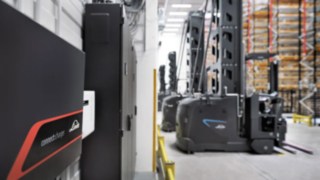
Lithium-ion trucks ensure an efficient flow of goods
Logistics performance is the second important factor in Hamm. Since the site went live in late summer 2022, Arvato has been storing and retrieving between 40,000 and 60,000 items per day for the beauty retailer Douglas. In total, the distribution center comprises around 520,000 storage locations in a carton warehouse and a further 8,000 in a pallet warehouse. The company relies on 17 semi-automated Linde K very narrow aisle trucks with lithium-ion batteries to operate this impressive facility quickly and safely. The man-up turret trucks with a lifting height of up to 18 meters run in two or three shifts depending on the season and are recharged during work breaks with Linde battery chargers. “Availability is absolutely essential with our high number of goods movements,” emphasizes logistics expert Tibor Sevenheck. “That’s why we opted for powerful chargers and charge all the narrow aisle trucks at the same time during breaks, so that our people can easily get through the shifts.”
The problem of load peaks
In practice, however, it was these very charging processes that proved to be a challenge. Unlike conventional lead-acid batteries, which usually charge up slowly overnight, industrial trucks with lithium-ion batteries charge faster and therefore need much more power. “As a result, we had significant upward spikes in our energy load profile. This was suboptimal in terms of costs due to the grid fee issue,” explains Tibor Sevenheck. After all, the grid fees are partly based on the highest power consumption value recorded during the billing period. So the matter was brought to the attention of Linde MH network partner Neotechnik Fördersysteme from Bielefeld, who had already taken care of the delivery and commissioning of the Linde K trucks together with the manufacturer Linde Material Handling in 2022.
Intelligent charging management provides the solution
In discussions with the Linde Material Handling team, it quickly became clear that the Linde connect:charger battery charging management system was ideally suited to both ensuring operational capability and availability, while at the same time optimizing the load curve profile. The Linde fleet management solution module consists of innovative hardware and software components that work together to enable intelligent load management. All 17 chargers at Arvato were first equipped with hardware units to collect all the relevant data on the charging behavior of the forklifts and send it to a central management software. A digital dashboard then not only provides the logistics team with detailed insights into each individual process, but also allows them to set numerous parameters individually, such as charging time windows and power limits.
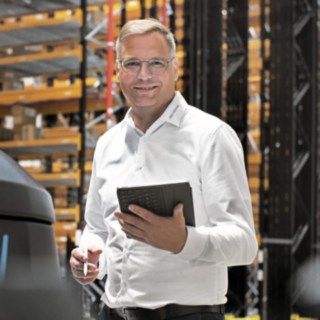
With the Linde connect:charger, we can individually control all 17 chargers and regulate the flow of electricity. Thanks to our technology, Arvato is making annual savings in the five-figure range.
Sven Wengh, Energy Expert, Linde MH network partner Neotechnik
No compromises in availability
“We have set a fixed load limit of 180 kW using the Linde MH application. In other words, the load profile is capped at this maximum value by the connect:charger, taking into account the charging process across every charging station,” explains Tibor Sevenheck. “And a reduced load profile ultimately means significantly lower grid fees for us. The annual savings are currently in the mid five-figure range,” says the Arvato logistics expert. At the same time, Linde’s battery charging management tool ensures that the trucks remain available despite the power limit. The connect:charger at Arvato was configured in such a way that it prioritizes the narrow aisle trucks with the lowest state of charge and allocates more power to the corresponding chargers. “This has absolutely proved its worth. The trucks are available when we need them without any loss of handling capacity,” confirms Tibor Sevenheck. “We’re even looking into the possibility of lowering the load limit even further in future.”
Further benefits are already in sight
Speaking of the future, the majority of Linde chargers are still connected to the central connect:charger control unit by cable. “In future, we would like to switch completely to the wireless version together with Linde MH,” says Tibor Sevenheck. Further milestones in terms of intelligent energy management are also already in the pipeline, such as the ability to configure dynamic load limits via the Linde charging management system and connect the connect:charger to the local building energy management system via a cloud solution. This would allow Arvato to integrate the charging data even more comprehensively into its resource planning and also make optimum use of the solar power from the PV system on the roof of the distribution center for charging its trucks and further optimizing its self-consumption ratio. On sunny days, the charging power can then be dynamically adjusted upwards by the connect:charger. “We expect this to add further value in terms of processes and costs,” emphasizes Tibor Sevenheck, adding: “Overall, however, we are already pretty close to the optimum in terms of energy thanks to connect:charger and the exceptional support from Linde MH.”
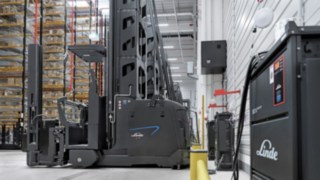
Arvato
Arvato is an innovative and internationally leading service provider in the field of supply chain management and e-commerce. It is a wholly owned subsidiary of Bertelsmann SE & Co. KGaA. Around 17,000 employees across 100 sites work with state-of-the-art technologies for global customers from the consumer products, tech, healthcare, automotive, and publisher sectors. Arvato provides logistics and fulfillment services for Douglas GmbH in its distribution center in Hamm, North Rhine-Westphalia, which was built in 2022 and covers around 32,000 square meters. A total of 17 Linde K trucks are in use, whose charging behavior is controlled by the ‘Linde connect:charger’ battery charging management system. Service is provided by the Linde MH network partner Neotechnik Fördersysteme from Bielefeld.