Measurably improved processes with the Linde Warehouse Navigator
Sparking an Idea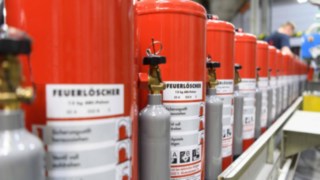
A new rack system, more space and new industrial trucks were on the wish list. This resulted in a complete system change to digital warehouse management using Linde Warehouse Navigator – including practically error-free order picking, reduced supply times and increased satisfaction. A visit to the fire protection specialist FLN Neuruppin.
Whether it was right to make a change is usually demonstrated at a specific moment, namely when you ask yourself how you managed before. At the fire protection specialist FLN Neuruppin, this moment has been happening almost daily since May 2021: “Today none of our team would want to do without the Linde Warehouse Navigator,” states Florian Sommerfeld, Logistics Manager of the company, which produces well over half a million fire extinguishers for Germany and the whole of Europe every year. Ultimately, the warehouse management system implemented during a complete reorganization has resulted in noticeable and measurable process improvements.
Looking Beyond the Requirements Specification
“Here we send both fully and partially picked pallets for dispatch, for example with foam extinguishers and CO2 extinguishers. These, like our production material, were stored distributed throughout a wide-aisle warehouse with 800 pallet spaces,” explains Sommerfeld. In order to know what the staff had to transport where and when, they used to have to deal with Excel lists and index cards. Originally, changing this was not on the agenda. Sommerfeld says, “we wanted a narrow-aisle warehouse to create more space, new industrial trucks and more efficient intralogistics.” With this requirements specification, they approached the Linde MH network partner TRAFÖ which took the opportunity to also examine the underlying logistics processes at FLN.
Tracking Down the Error Sources
Project Manager Michael Batz and Michael Brüning from TRAFÖ recount that “if a customer wants to make an investment, it should pay off in the short and long term. In the case of FLN, during the project work it fairly quickly became clear that only the combination of new hardware and software would really work smoothly.” This is because there was definite room for improvement in terms of smooth operations. As FLN warehouse technician Florian Hartlep explains, “For us drivers, the biggest problem with the old warehouse management was how long everything took. For every new picking order, we had to manually collect the right ticket from a file, get into the forklift truck, manually look for the shelf and pack the goods onto the pallet.” In short, there were lots of interfaces, a high level of documentation work and corresponding potential for error.
Now there is seamless warehouse stock with optimum distribution of driving jobs
Always know what is where and which goods are stored where for which order. Lots of questions that can be answered with the help of a digital ‘warehouse specialist’, namely Linde Warehouse Navigator. The smart tool is networked to the FLN ERP system and displays the entire stock level in real time. This is made possible with barcode labels created for every pallet – for incoming raw materials as well as finished palletized extinguishers, which leave production on a conveyor system. From the first time the label is scanned, the pallets are ‘married’ to the system, i.e. recorded in the Linde Warehouse Navigator. This means that the software can distribute transport jobs optimally and send them to the terminals in the two new Linde K trucks. The mechanically managed man-up trucks then navigate the employees semi-automatically to precisely the right shelf.
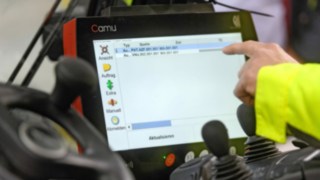
Get the job ticket, find the shelf: that’s a thing of the past.
FLN warehouse technician Florian Hartlep describes the new process: “At the shelf, I take the goods, scan to confirm this at each location and leave the pallet at the handover point. That’s it!” In addition to the new narrow-aisle warehouse with its 1,600 spaces, the Paternoster small-parts warehouse is also connected to the Linde software. “For example, our employees take spare parts included in the order from here, pick them manually and put them on the right pallet,” explains Dennis Bialek, Logistics Foreman. The employees are told which compartment of the Paternoster storage system the product is in on a mobile hand-held terminal. “Any removals are also confirmed by scanning here, meaning that incorrect deliveries are almost excluded,” adds Bialek.
Digitalization Pays Off in Many Areas
The bottom line is that as a result of the reorganization and digitalization of the warehouse, incorrect order picking has reduced by almost 90 percent, “not to mention the time that we used to have to spend getting things ready,” Logistics Manager Sommerfeld comments happily. “Today, if a customer orders by 10 a.m., our people can have the order ready to be sent out on the same day. This would hardly have been conceivable before – and the same is true for the inventory, which one team member now does in one day.” In addition, sales colleagues can now provide customers with clear information and even make changes to the order right up until just before it is sent out, which is all made possible by the real time display of the stock levels and order status.
Remote Go-live
Today, seven months after the reorganization, the new processes have long since become second nature to the FLN logistics team. “From start to finish, the project was a complete success for us,” assesses Logistics Manager Sommerfeld. “However, this is partly due to the fact that we actively involved our people in the reorganization from the outset.” This meant that, among other things, employees were able to contribute ideas which, in combination with comprehensive online training, ensured a high level of acceptance and confidence. “The close collaboration with our Linde MH network partner TRAFÖ even meant that it was possible for the entire go-live to be handled remotely,” says the FLN Logistics Manager with satisfaction.
Promising Interface for the Future
”We have really taken a huge step into the future here,” Logistics Manager Florian Sommerfeld says finally encapsulating the matter. Talking of the future, there could be further automation at FLN any time soon; after all the system architecture of the Linde Warehouse Navigator makes it easily possible, for example to integrate driverless transport systems into the goods flow. “Something like this would be ideal, for example, for the transport route between production and the warehouse, and we have already had initial discussions about this with Linde Material Handling and our network partner TRAFÖ. I think that with this we already have the next spark of an idea in the pipeline,” adds Sommerfeld with a grin.
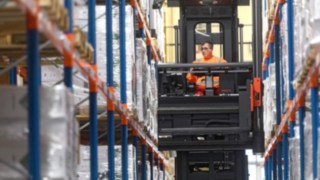
FLN Neuruppin
FLN Neuruppin is part of the Fire Suppression Products business unit of the internationally operating company Johnson Controls. The site in Neuruppin, in the German state of Brandenburg, has been producing mobile fire extinguishers for over 100 years for customers from a wide range of sectors, from the chemical industry to mining, and from educational institutions to data centers. Two Linde K-modular Very Narrow Aisle Trucks with navigation as well as one Linde E16 and two Linde MT15 are used for the internal flow of goods in the warehouse. The pallet narrow-aisle shelving system that was newly installed in 2021 also has gravity-activated roller conveyors and a roller belt; the company uses the Linde Warehouse Navigator for warehouse management.