Safety approach: smart investments, longterm paybacks
Heineken Switzerland: More Safety in Intralogistics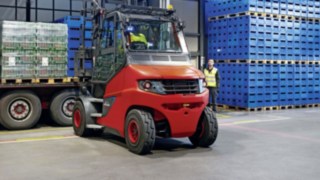
Since 2017, Heineken Switzerland has been minimizing risks in its internal material flow, preventing accidents, and keeping processes running continuously—thanks in large part to the Linde Safety Guard. The company was one of the first to introduce the safety assistance system at the time, and is a true safety pioneer.
Majestic, mighty, immovable—when you look to the north-west from Chur in Switzerland, words like these are certain to spring to mind. The Calanda massif rises to an imposing 2,084 meters here, towering over the canton’s capital of Graubünden in silent grandeur. But while this natural bastion might well convey a sense of safety, this isn’t something that’s taken for granted at the two Heineken Switzerland properties located at the foot of the Calanda massif in Chur and the neighboring municipality of Domat/Ems—far from it. “At management level, we believe it’s our responsibility to ensure that all employees return home safe and sound after work,” says Warehouse Manager Gian-Carlo Bissegger. “In terms of our intralogistics, this means that we use the right technical solutions to pursue our vision of an accident-free workplace, one step at a time.”
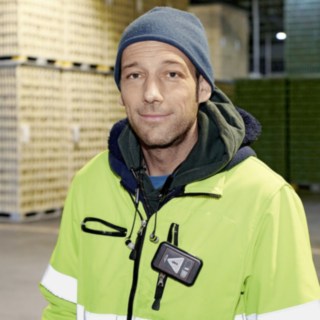
We’ve been working with the Linde Safety Guard for seven years now and are still completely satisfied. One thing we especially like is that we can add modules to the assistance system to suit our conditions here on site.
Gian-Carlo Bissegger, Warehouse Manager, Heineken Switzerland AG
A Clear Mission: More Safety in Intralogistics
Heineken Switzerland is a textbook example of how combining personal conviction with technical innovations can drive safety in intralogistics in a multitude of ways. The brewery was one of the very first companies to opt for the Linde Safety Guard assistance system, which had just been launched on the market. “At our two sites, people sometimes work in close proximity to forklift trucks—which can get quite confusing. We handle around 1,500 pallets a day at our Chur production facility alone, and around 2,000 more in our main warehouse in Domat/Ems,” explains Warehouse Manager Bissegger. The brewery uses heavy-duty 8-ton counterbalanced forklift trucks of the Linde H80 and Linde E80 types with a 4-way pallet handler for in-house transport. “After running into a number of tricky situations, we said: We cannot and do not want to take this risk any longer,” stresses the logistics specialist.
Assistance System from Linde Material Handling Boosts Safety in Goods Handling
As we all know, there are plenty of warning solutions for logistics applications to choose from. But a real highlight of the Linde Safety Guard, which also impressed Heineken Switzerland at the time, is the innovative way the system works. The technical basis consists of special transmitter and receiver units that communicate with each other via interference-free signals in the ultra-wideband range—even through doors and shelves. Boasting an accuracy of ten centimeters, the positioning system only triggers a warning if there is a real threat of danger. “The Truck Unit installed in the forklifts allows operators at Heineken to see how many people are approaching the truck and from which direction. The pedestrians in turn carry a Portable Unit, which uses acoustic warnings, LED lights, and vibrations to draw their attention to a potential danger from a forklift truck in the vicinity. And forklift drivers are alerted the same way when a colleague approaches,” explains Markus Muffler, Head of Service Sales & Product Management at Linde Material Handling Switzerland.
Safety in Intralogistics: Always Room for Improvement
The Linde Safety Guard has been operating reliably at the two Heineken sites for the past seven years now. “The solution was customized to fit our needs and has significantly increased operational safety in our halls and outdoor areas,” sums up Warehouse Manager Bissegger. Even so, those in charge rightly believe that they have yet to reach the pinnacle of safety. “Safety is a never-ending journey—you have to continually adapt to new challenges and look for improvements,” notes the logistics expert.
Artificial Intelligence Boosts Safety in the Warehouse
The company recently implemented one such improvement together with Linde MH at its main warehouse in Domat/Ems. “Our warehouse has a critical juncture where forklifts and people from outside the company regularly come into contact. So it would have been difficult to implement or control the use of Portable Units,” says Bissegger, describing the situation. A special networked camera that permanently monitors the area is now being used to alleviate the situation. If a person enters the area at the same time a forklift truck approaches, a ceiling projector casts a clearly visible warning symbol onto the hall floor. At the same time, the truck operator receives a corresponding warning via the Truck Unit and the truck’s speed is slowed to 2 km/h.
Assistance System for Forklifts Features Modular Add-ons
“For me as a driver, the Linde Material Handling system is a huge help, because you basically always have a passenger keeping an eye on you,” says forklift driver Paul Misetic with satisfaction. Heineken Switzerland is also looking to the Linde Door Control as a further means of support. This expansion module of the Linde Safety Guard precisely adjusts the speed of the forklift trucks to the opening mechanism of the high-speed doors. One major advantage is that the system can be individually configured in conjunction with highly accurate positioning down to the centimeter. “The door only opens when the forklift driver actually wants to drive through it. If a forklift truck drives past, nothing happens,” says expert Markus Muffler from Linde Material Handling Switzerland.
Increased Safety in Intralogistics Reduces Costs
According to current plans, Linde Door Control is to be installed in Chur from 2025. “Another key element in our carefully designed safety approach,” notes Heineken Warehouse Manager Bissegger, while noting that such purchases always involve a certain financial outlay. “But when you consider the potential consequences that just one accident can have—damage to trucks, infrastructure, and goods, downtime or, in the worst case, even impacts on the health of those affected—then there is really only one logical conclusion. The way to minimize costs isn’t by doing without safety systems like these in intralogistics, but by making a conscious decision to use them.” It’s an approach that those in charge at Heineken are definitely aiming to stick to in the future.
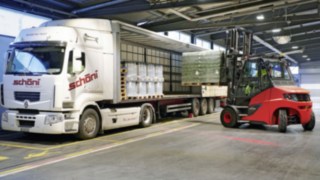
Heineken Switzerland AG
Heineken Switzerland AG is part of the global Heineken Group, which is the second largest brewery group in the world (in terms of the quantity of beer produced). The company has been based in Switzerland since 1984 and operates another production facility in Lucerne in addition to Chur; it also has a total of 16 sales and logistics sites. Brands marketed by Heineken Switzerland include classic Heineken as well as traditional beer Calanda and various international specialties. The company manages intralogistics at the Chur site as well as at its site in Domat/Ems, just a few kilometers away, using five Linde H80 and Linde E80 counterbalanced forklift trucks with a Li-ION Drive.