Radeberger Group backs electric forklift trucks
Who Dares Wins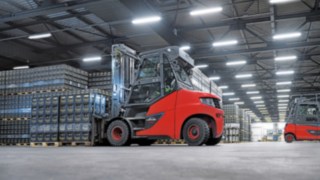
The first step does not have to be the hardest, even when heavy loads come into play. In 2015, the renowned Radeberger Group, working with Linde Material Handling, was one of the first companies in the beverage industry to move from internal combustion engines to electrically powered trucks—right up to the highest payload classes. This decision would prove to be spot-on in several respects.
Daring to venture into unknown territory can be the start of an amazing story. Just like in Radeberg near Dresden (Germany) in 1872, for example. Curiously, five gentlemen met in a wine shop, put their heads together and launched a special brewery. It was a brewery that would establish the previously largely unknown Pilsner brewing process in Germany. “Admittedly, our plan was not that visionary, but we have always been pioneers,” says Jens Berberich. He heads the main Procurement, Logistics and Sustainability department of the Radeberger Group, Germany’s largest private brewery group. As early as 2015, they decided to convert the forklift fleet to climate-friendly electric propulsion.
Large Fleet, High Tonnage—and Huge Potential Savings
The Radeberger Group operates numerous production and filling sites in Germany; in addition, the company, which is also active in beverage wholesale, long-haul logistics, beverage retail and other areas, also has logistics centers and other properties. “Across the Group, we operate around 300 forklift trucks, from 1.5-metric tonne to heavy 8-metric tonne trucks,” says Wolfgang Klee, Head of Logistics at the Radeberger export brewery. Until 2015, the diesel and propellant gas fleet emitted around 9,300 metric tonnes of CO2 per year. This figure was very challenging for the people in charge—as Jens Berberich highlights: “As a food manufacturer, we believe that we have a particular obligation to protect nature and natural resources; and anyone who really wants to become more sustainable has to start by reducing emissions. After all, we do not have to compensate for anything that we do not emit.”

In the high payload classes in particular, almost nobody in our industry had ventured into battery power units in 2015.
Jens Berberich, Head of the main Procurement, Logistics and Sustainability department of the Radeberger Group
A Pioneer Meets a Debutant: Radeberger Invited the Linde E80 to the Internal Competition
“The call for tenders from the Radeberger Group in 2015 was something special even for us,” says Christian Kunkel from Linde MH network partner Suffel Fördertechnik, who oversaw the project together with Nils Bielmann from Willenbrock Fördertechnik. “The tender practically coincided with the market debut of the Linde E80 with lead-acid battery, so we were not yet able to provide the customer with many references for this device category.” Accordingly, the Linde experts were curious to see how these new powerhouses would fare in direct comparison with the electric forklift trucks from other manufacturers. “We started an internal competition, not only so that we would be able to compare numbers—it was at least as important for us to get concrete feedback from the forklift drivers,” says Jens Berberich, who was the person in charge from the Radeberger Group.
3,000 Operating Hours per Year: The New Truck Excels in Long-term Testing
The staff were particularly impressed by the ergonomics and sensitivity of the Linde E80. After the forklift truck had won this race, the new electric model also performed really well in the one-year long-term testing at the Krostitz site. “With more than 3,000 operating hours within twelve months, we did not do the Linde electric forklift trucks any favors; at the same time, we were always in close contact with the Linde project team and were able to state our particular needs—for example, in terms of air conditioning and heating. The support from Linde was really top-notch,” says Jens Berberich.
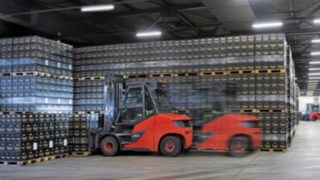
It’s Even Better with Li-ION Technology
Back to today—and directly to Radeberg. Here, where the brewing vessels only produce Radeberger Pilsener and Radeberger Alcohol-Free with real Pilsner character and locally grown Callista aroma hops, you can see red forklifts whirring back and forth everywhere. “In two-shift operation, we handle 20 full and empty trucks per hour at absolute peak,” says Head of Logistics Wolfgang Klee. The electric 8-metric tonne trucks now get their energy from lithium-ion energy storage systems. “By 2026, we will only be using Li-ION devices from Linde—and thanks to the higher energy efficiency, we will reduce our carbon footprint by a further 30 percent,” emphasizes Jens Berberich. This will also mean that there will be no need for the time-consuming process of changing the lead-acid batteries. The fact that the Radeberger Group is already using 80 percent green electricity throughout the company and also wants to gradually increase the proportion of self-generated energy rounds off the project perfectly.
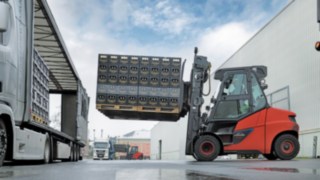
From Combustion to Electric: Switching Requires a New Way of Thinking
It is a fact that anyone who uses new technologies will usually also have to give up old habits in daily life. “When we were using combustion engines here in Radeberg, one person would use the same truck throughout a shift. Due to our high work intensity and the sometimes-long distances, this was no longer possible with the electric forklift trucks,” explains Head of Logistics Wolfgang Klee. However, they worked with the Linde project team to quickly find a solution to this challenge, in the form of an individual charging logic.
The Combustion Engines Are Not Missed
“We carry out interim charging for the devices each day during work breaks at 9 a.m. and 6 p.m. for half an hour each. We have also defined specific threshold values for the forklift trucks. If the battery charge status drops below this level, the trucks come to the chargers and you simply switch to another device with a higher charge status,” explains Wolfgang Klee. The Head of Logistics goes on to add that this system has quickly become second nature to the team, meaning that the required handling capacity is easily achieved: “A Linde E80 with a 6-way handler processes a complete truck in less than ten minutes. Our people work with the forklift trucks just as if they had never driven anything else. And I no longer know of anyone who wants the combustion engines back.”
In order to ensure that we have access to charged trucks at all times, we have created an exact schedule of when each electric forklift truck comes to the charging station.
Wolfgang Klee, Head of Logistics at the Radeberger export brewery
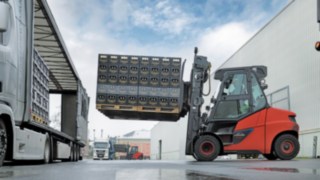
Radeberger Group
The company Radeberger Group is part of the family business Dr. August Oetker KG and, with well-known brands such as Radeberger, Schöfferhofer, Clausthaler, Jever and many more, is Germany’s largest private brewery group. Internationally, the products are exported to over 70 countries—traveling as far as Chile. The Group also operates in the areas of beverage wholesale, long-haul logistics, beverage retail and system solutions for the catering industry via various subsidiaries and shareholdings. When it comes to intralogistics, the company has long relied on the equipment and expertise of Linde Material Handling throughout the Group. During a call for tenders in 2015, the industrial truck fleet that had developed over time was harmonized, electrified and Linde was selected as the single supplier. In total, there are around 300 Linde forklift trucks with a range of tonnages in use; when warehouse technology is included, the entire fleet comprises around 1200 devices.