Better warehouse management overall with the Linde Warehouse Navigator
Seeing Everything, Everywhere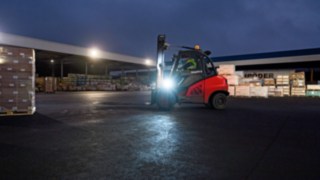
We all know transparency trumps all in contract logistics. Even better if this can be generated as efficiently as possible: Transport and logistics service provider Gebrüder Schröder GmbH & Co. KG relies on the Linde Warehouse Navigator, which not only speeds up and simplifies processes on site, but also visualizes stock levels in real time for customers too.
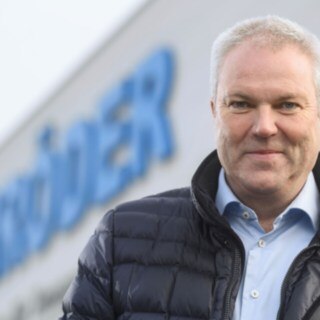
Joachim Altmann, Managing Director of Gebrüder Schröder GmbH & Co. KG, is clearly happy when he talks about the up and downs of his business. After all, they are very particular ups and downs, as he explains with a smile at a meeting in person in Ebernhahn in the German federal state of Rhineland-Palatinate. “Value creation has been going up since October 2021 and expenses have been going down. It just goes to show once again that we are essentially always open to the new while maintaining our tradition.” The “new” for the family-run medium-sized transport and logistics service provider established in 1939, includes warehouse management using the Linde Warehouse Navigator.
Transparency is the central keyword
“We handle national transport for our customers as a service provider and also offer warehouse management as part of that,” explains Altmann. One of the company’s focuses is building materials, particularly tiles. “The overview of current stocks and individual batches can sometimes not be good enough there—for us or our clients.” So when it came to the new construction of a warehouse scheduled for 2019, thoughts also turned to the implementation of a new warehouse management system. Project manager Jörg Hoffmann remembers: “In 2019 we went to our Linde MH network partner Jungbluth Fördertechnik with our initial request. It was important for us to get everything from one place: trucks, rack system, and software.”
Data Combined with Linde System
Now the warehouse and rack system are in place, as well as the software system. Put another way: It’s running like clockwork, as the saying goes. “We kicked off with the Linde Warehouse Navigator for a customer in the new indoor warehouse. The processes are relatively simple here: pallets in, pallets out,” says project manager Hoffmann.
When a truck arrives in the yard, the forklift truck drivers scan the customer label with all the relevant info—from item number to batch to weight. These data are then “married” with the Linde Warehouse Navigator using a unique TU number generated on site (transport unit number). In the warehouse, the employees decide on the storage location, benefiting once again from a smart idea from the Linde MH network partner.
Stock levels can be viewed at any time.
Project manager Hoffmann explains: “There are barcodes on the racks at eye level, structured using a traffic light system. Red for top, yellow for middle, green for bottom. So when colleagues are storing items high up with their Linde reach trucks , they can still easily scan at eye height with the scanner guns.” When the storage level is confirmed, the Linde Warehouse Navigator knows where to find which goods. The trick here: “This information isn’t just available in-house; customers can view their stock levels remotely at any time via a special interface,” Hoffmann is pleased to say.
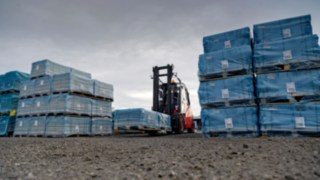
Outdoor warehouse also finally paper-free
The thinking at Schröder was that if it’s working well inside, let’s do it outside too. “We use our huge outdoor area to store tiles for a second large client, among other things. The situation is more complex here, because we are order picking and are also reliant on exact batch management,” says Hoffmann. And of course, tiles are natural products. When an end customer re-orders the same tiles for the same project, these must come from the same batch, so that there are no differences in color shades. It sounds relatively challenging logistically—and it was, until the introduction of the new warehouse management system, as Bernd Heinz, warehouse logistics team leader, confirms: “I had to keep fighting my way through sheets of paper and site maps to find what was out here or where each batch was.” Today, the whole process is much easier and entirely paper-less.
The tablet in my Linde forklift truck shows me the entire outdoor warehouse with all relevant information and brings up the transport jobs. I know exactly where I need to collect how much of what item for an order.
Picking orders come directly to the forklift truck
The basic principle with the barcodes matched by the Linde solution for the outdoor warehouse is the same as the one used indoors. After “marrying” the first two codes, the drivers can choose any storage location which is then confirmed by scanning a third label, here shown attached to a bollard. Heinz: “The tablet in my Linde forklift truck shows me the entire outdoor warehouse with all relevant information and brings up the transport jobs. I know exactly where I need to collect how much of what item for an order.”
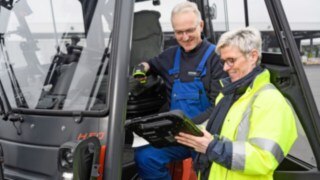

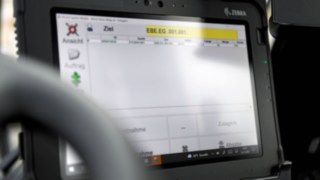
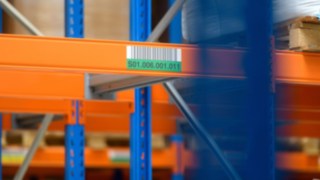
The system is extremely flexible
Schröder logistics professionals are convinced by the high flexibility of the Linde technology: If the system is showing a TU for retrieval, it can be replaced with a different TU in the system on site. “That’s a major advantage, because we store in blocks here and I might not be able to get through to a product with my truck.
If the same product is easier to reach somewhere else, I can enter this accordingly. The system would object if it was the wrong item or wrong batch. So errors are pretty much impossible for us here,” reports Heinz. Managing Director Joachim Altmann adds: “At the same time, our clients are pleased that they can see everything here like they can indoors; for example, they can check up on batches and items far faster than ever before.”
All working smoothly
The overall situation since the go-live in October 2021 is clear and has concrete facts to back it up. Schröder Managing Director Altmann sums it up: “By ending manual order entry alone, we are saving about four hours of valuable working time a day.” And while we’re talking savings: there’s also no need to reorganize the outdoor warehouse because the Linde Warehouse Navigator can be adapted exactly to individual needs by the network partner. “Everything comes together perfectly here in one smooth process: from the rack to the reach mast to the robust 5-ton trucks outside. And above all our digital warehouse management. Overall, everything runs faster, more transparently, and practically error-free.” In future, says Hoffmann, it is likely that further clients will be integrated into the Linde Warehouse Navigator. “After all, I don’t know any customers who wouldn’t be happy with the principle of ‘costs down, value creation up’.”
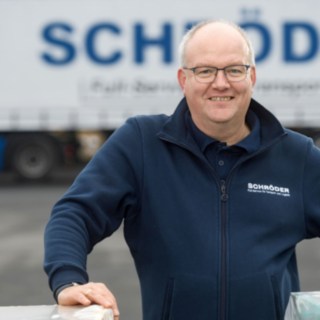
Gebrüder Schröder GmbH & Co. KG
Gebrüder Schröder GmbH & Co. KG is an owner-run medium-sized transport and logistics service provider based in Ebernhahn near Koblenz in Germany. The company offers a wide range of logistical services, up to and including the transportation of dangerous goods, to its customers, who include the building materials, chemical, food, and pharmaceutical industries. For its intralogistics, Schröder has relied for years on Linde technology and know-how, for example the Linde H50 5-ton counterbalanced forklift truck, Linde R14 reach trucks and, since August 2020, the Linde Warehouse Navigator warehouse management software.