Seifert counts on DMC to boost productivity and safety
Higher is Faster Here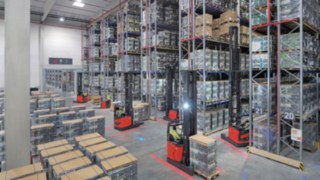
The products of a well-known gardening tool manufacturer are stored up to 13 meters high at the Seifert Logistics Group in the north of Ulm, (Germany). Yet despite this considerable height, the reach trucks not only load and unload the shelves extremely quickly, but also extremely safely. This is mainly thanks to Linde’s Dynamic Mast Control (DMC) assistance system.
In the world of contract logistics, it is sometimes the tiniest details that make all the difference – even if they measure no more than a millimeter. At the Seifert Logistics Group, this millimeter holds great significance. For over three quarters of a century, this family-run contract logistics company from Ulm has been living by the philosophy of always providing customer companies with that little bit more. With regard to its location in the north of the Münster, which opened in 2022, the “Seifert millimeter” could now also be expressed in seconds. Or, 17 seconds, to be more precise. Thanks to Linde technology, this amount of time can be saved during every storage and retrieval process in the warehouse.
In Ulm, People Think Big and Build Big
Take, for example, what Seifert himself describes as the most extensive single project in the company’s history: “In our new complex, we have created around 50,000 square meters of storage space and around 100,000 pallet spaces,” explains Julian Seifert, Head of Standardization & Digitization, describing the impressive dimensions of the multi-user logistics center. Behind the hall walls, Seifert stores products for companies including a leading manufacturer of garden tools and takes care of the entire supply chain management for this company.
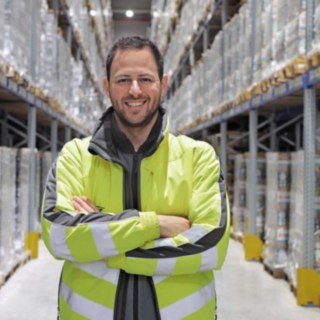
In our new logistics center, we wanted to make the most of the space –which is why our shelves are up to 13 meters high.
Julian Seifert, Head of Standardization & Digitalization at Seifert Logistics Group
When Everything Begins to Bloom, So Does Business
That’s why the company places high demands on the industrial truckswhich are responsible for the storage and retrieval of the palletized goods: “Reach trucks were clearly the first choice for us; however, it was essential to ensure that our employees could work at these heights not only as safely but also as productively as possible; after all, the garden equipment sector experiences extreme seasonal peaks at times,” explains Julian Seifert, summing up the situation. And so, before the new site was commissioned, models from various providers were invited for testing – including the Linde R20 with Dynamic Mast Control.
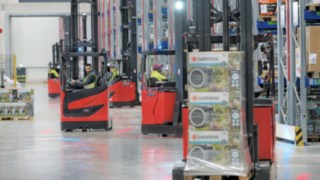
Which Reach Truck Will Come out on Top?
If you visit the high-ceilinged halls of Seifert today, you will see countless red trucks buzzing around between the colossal shelving structures packed to the rafters with goods. A total of 21 Linde R20s effortlessly extend their masts up to the sixth rack level and maneuver the pallets quickly and safely from A to B. Alexander König, Key Account Manager at Linde MH network partner Schöler Fördertechnik, explains why the equipment from Aschaffenburg won over the Seifert team: “The decisive factor was the Dynamic Mast Control; when compared with competitor models, it was clear that Linde technology offered tangible advantages when dealing with storage heights from around seven meters.”
Intelligent Technology is Making the Difference
The Linde system is based on a high-precision electric drive and sophisticated sensor and control technology: A central control unit continuously receives sensor data on mast vibration and information on lifting height and load weight. Based on this information, control signals are transmitted to the electric drive, which then compensates for both the bending and oscillation of the mast with targeted counter-movements. Logistics expert Marcel Hoffmann describes what this feels like in practice: “With conventional trucks, you always have to wait until the mast has stopped swaying. This is not the case with Linde trucks at all – storage and retrieval works without much shaking. This means it’s much more effective and relaxing to work with.”
Productivity meets safety – a good match
Compared to reach trucks with a conventional hydraulic drive, the resulting productivity advantage is around 17 seconds per loading process. “With the high number of trucks and processes, this quickly adds up,” confirms Schöler expert Alexander König. Added to this is the extra safety that the Linde Safety Guard provides. Finally, all Linde R20s are equipped with the innovative safety system, which precisely locates operators and pedestrians and alerts them of each other’s presence. Julian Seifert concludes: “We were impressed with the technology Linde MH has to offer, but also with the Servicing from Schöler. You could say: This is precisely the extra millimeter that we have been committed to delivering for over 75 years.”
Thanks to DMC, damage to pallets or goods is virtually non-existent.
Julian Seifert, Head of Standardization & Digitalization at Seifert Logistics Group
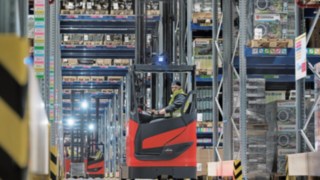
Seifert Logistics Group
Now in its third generation of family management, the Seifert Logistics Group is one of the top 100 logistics companies in Germany. Around 4,000 employees at more than 45 locations work in several core business areas: In addition to providing traditional contract logistics, Seifert is also active in transportation, silo and tank cleaning as well as in the segment of industry-specific value-added services. In 2022, the company opened its new multi-user logistics center in the north of Ulm, where Seifert has a total of 53 Linde MH industrial trucks including 21 Reach trucks of the type Linde R20 with Dynamic Mast Control. Enhanced safety in the internal flow of goods is provided by the system Linde Safety Guard. The local Linde MH network partner Schöler Fördertechnik takes care of the service and maintenance of the truck fleet.