Automotive industry
Automotive: Material Flow in Transition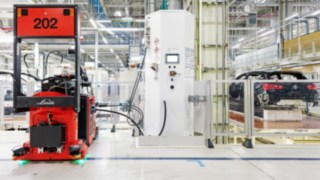
Hardly any other industry is under such radical pressure to renew itself these days as the automotive industry. Social change and regulatory intervention are changing the traditional markets and forcing car manufacturers to undergo far-reaching transformations. In order to cope with this change, companies are investing in new business models, from electric drives to car sharing and mobility services. These innovations are generating massive cost pressure, which is being countered with savings programs and measures to increase efficiency.
Challenges for the automotive industry
On closer inspection, four core areas can be identified that have become of central importance for the automotive industry in recent years.
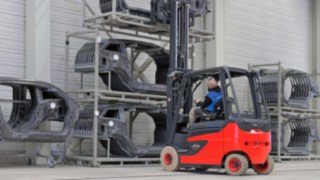
Intralogistics as a driver of change
Many car manufacturers have discovered intralogistics as a pioneering factor in their transformation. As the “last mile” of the supply chain, it links inbound logistics with production. As the oil that keeps the cogs of the production line turning, it is largely responsible for the overall efficiency of the plants of automobile manufacturers and their suppliers. At the same time, the vehicle fleets of original equipment manufacturers (OEMs) together with the fleets of their Tier 1 and Tier 2 suppliers offer great potential for CO₂ savings.
Here we showcase the technological innovations and consulting services from Linde Material Handling that provide solutions to all four core challenges facing the automotive industry.
Ensuring the flow of production
The automotive industry is considered a pioneer in successful process optimization with advanced intralogistics systems. By manufacturing according to the principles of “Just in time” (JIT) and “Just in sequence” (JIS), manufacturers minimize stock levels and ensure that components are delivered directly to the assembly lines on demand and in a specified sequence. For many Tier 1 suppliers, their own plant is located in close proximity to the original equipment manufacturer’s assembly plant. In fact, both plants are often located on the same site, which is why forklifts and order pickers are used to move materials between the assembly lines.
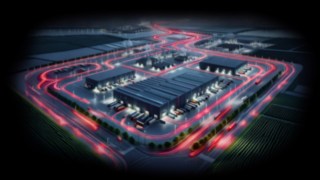
This complex ecosystem requires state-of-the-art digital solutions that localize the flow of goods and information, and seamlessly integrate suppliers and 3PL service providers into the production process. On the other hand, ergonomic forklift trucks and warehouse handling equipment ensure each truck operates with maximum efficiency. The following solutions from Linde Material Handling help to ensure the production flow in the automotive industry.
- Efficient control of the fleet with the Linde MH fleet management system
- A big variety of tractors and tugger trains to keep production lines fed
- Digital warehouse management and forklift guiding system
- Worldwide access to a broad offering of short-term rental vehicles and used industrial trucksto ensure maximum fleet availability
- Intuitive control concept with Linde Load Control and dual pedal control to maximize productivity
- Trucks developed to the highest ergonomic standards for driver protection and maximum throughput
Minimizing costs
The fundamental transformation currently taking place in the automotive industry is exposing many manufacturers to immense cost pressure. The changeover to new drive systems in particular is posing enormous challenges for car manufacturers. Global automakers have embarked on a rigid austerity course in order to reduce running costs, and well-known suppliers are also adapting their structures to the changed market conditions. The realization is gaining ground that logistics and intralogistics can be powerful cost reducers.
Increased throughput reduces costs just as efficiently as safety solutions that prevent damage to materials and people. The possibility of being able to fall back on rented, leased, or used industrial trucks if necessary also has a dynamic effect on the cost structure.
The following solutions from Linde MH can effectively reduce costs in intralogistics:
- Safety as a cost-saving factor (trucks and workers)
- Consulting for fleet optimization
- Service as a cost-saving factor
- Financing as a cost regulator (leasing, rental, or hire purchase)
- Used trucks for less intensive applications
- Energy costs can be cut by switching to Li-ION or fuel cells, or efficient charging management with connect:charger
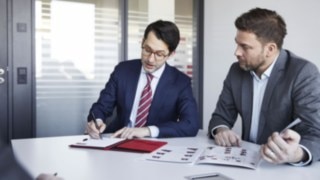
Automated intralogistics in the automotive industry
The automotive industry is characterized by its innovative strength – and the same is true for intralogistics processes. Like JIT and JIS manufacturing, the Kanban method for production control also has its origins in the automotive industry. In order to optimize their internal logistics, manufacturers have long since turned to automation and modern IT solutions. The internet of things, big data, and cloud computing are used in conjunction with automated guided vehicles (AGVs) in the automotive industry to achieve significant efficiency gains in the distribution process through tracking, identification, and status monitoring.

The automotive industry ensures the supply of production lines and assembly workstations largely through semi-automated or automated transport with tugger trains. Thanks to the high degree of maturity of their own intralogistics expertise, automotive manufacturers are constantly looking for technical innovations that optimize both the automation capability of individual trucks and the automation of entire process sections. These efforts are supported by the innovative technologies of Linde Material Handling.
Protecting the environment
Against the background of climate change, social and political developments are putting the automotive industry under immense pressure to change. CO₂ taxes and emissions trading are forcing manufacturers to act. Not only must they increasingly develop alternative forms of drive such as electric and hybrid vehicles, but they also need to establish climate-neutral supply chains and production processes.
The calculation is now very simple: CO₂ emissions cost money, CO₂ reduction saves money. In addition to raw material extraction and material production, the emissions linked to internal intralogistics are increasingly becoming the target of reduction measures. If forklifts and warehouse equipment are converted to modern electric drives or As a pioneer in the fields of electrification, lithium-ion drive and fuel cell technology, there is enormous potential for savings. Linde Material Handling offers numerous innovative solutions for a better carbon balance. Furthermore, the use of HVO fuel in diesel forklift trucks from Linde MH enables an immediate reduction in CO₂ emissions. HVO stands for hydrotreated vegetable oil and is produced entirely from renewable raw materials such as waste and residual materials, which significantly improves the environmental footprint. In view of stricter regulations for CO₂ emissions, switching to HVO can be a sensible transition technology towards electrification.
In order to establish climate-friendly supply chains, automotive manufacturers are also constantly looking for partner companies who manufacture their products in an environmentally friendly manner and disclose the ecological balance of their own production operations. In Linde Material Handling, they find a sustainable and transparent partner.
- Wide range of electric forklifts and trucks with electric drive
- Linde MH as an innovation driver with lithium-ion technology
- Fuel cell technology from Linde Material Handling
- Energy consulting, in particular with sustainability as a starting point
- Platinum rating for sustainability from the international assessment platform EcoVadis
- Linde MH products and services meet all automotive industry standards (NQC) and sustainability