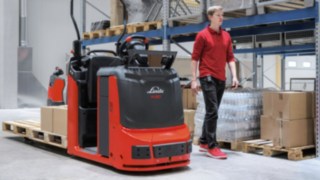
Saving time and energy in the order picking process
17 Jun 2021
New semi-automatic equipment option for N20 SA and N20 C SA order pickers from Linde Material Handling
The rate of productivity when order picking at ground level depends on the operator’s speed and precision. Short walking and driving distances save time and effort and increase the efficiency of the process. Logistics service providers and retail chains can now exploit this optimization potential using the Linde N20 SA and N20 C SA semi-automated order pickers, together with a new equipment option (semi-automated) that offers two drive modes in which the vehicles automatically follow the operator or drive ahead. As a result, employees are relieved of non-value adding activities and order picking performance can be boosted by up to 20 percent.
Whether carried out at a DIY store, a food wholesaler, an automotive supplier or a contract logistics company, order picking is labor-intensive, requiring stamina and alertness of warehouse staff. A substantial part of the process consists of the employees’ walking to the racks and back to the order picker. This is a time- and energy-consuming activity but, unlike picking goods from the rack and placing them on the load carrier, it does not create any added value. “Even a mere a few seconds expended during each handling operation adds up to a lot of time lost over the course of the workday, and just a few steps, repeated over and over again, add to operators’ fatigue and sap energy that would be better directed at completing the picking process without errors,” argues Philipp Stephan, Product Manager Automation & Intralogistics Solutions at Linde Material Handling (MH).
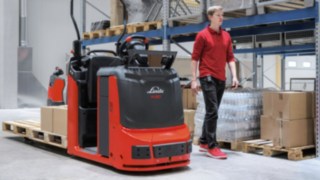
The new Linde N20 SA and N20 C SA semi-automated order pickers offer two drive modes in which the vehicles automatically follow the operator or drive ahead. As a result, employees are relieved of non-value adding activities and order picking performance can be boosted by up to 20 percent.
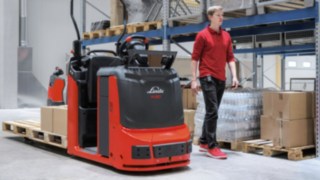
The new Linde N20 SA and N20 C SA semi-automated order pickers offer two drive modes in which the vehicles automatically follow the operator or drive ahead. As a result, employees are relieved of non-value adding activities and order picking performance can be boosted by up to 20 percent.
At the same time, the demands on warehouse staff continue to grow: Pick rates are expected to increase, error rates are to be reduced, and health problems prevented. As a result, the picking process offers great potential for increasing the overall efficiency of warehouse logistics – optimization potential that can now be tapped using the SA option of Linde order pickers with up to 2.5 tons load capacity. This is because both semi-automatic drive modes aim to significantly shorten travel and walking distances during order picking in the aisles. At the same time, there is no longer any need to constantly climb on and off the vehicle, which reduces the risk of accidents. This has positive effects on handling performance and productivity in the warehouse.
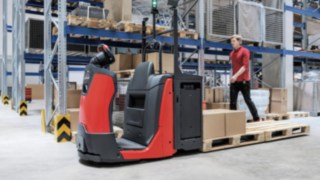
The semi-automated option of Linde order pickers N20 SA and N20 C SA with up to 2.5 tons load capacity aim to significantly shorten travel and walking distances during order picking in the aisles.
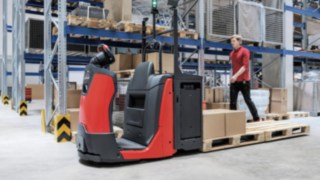
The semi-automated option of Linde order pickers N20 SA and N20 C SA with up to 2.5 tons load capacity aim to significantly shorten travel and walking distances during order picking in the aisles.
Walks along and drives ahead
One of the most common processes that take place in high rack warehouses is that of picking on one side of the rack, during which an employee walks along the aisle and back. This activity is supported by the accompanying vehicle’s semi-automatic “follow-me” function. If the operator stops, the vehicle stops as well, allowing them to place the goods directly from the rack onto the pallet. If the operator continues to walk, the truck also continues moving forward. In this way, the employee moves along the rack and collects the goods without constantly having to walk to the driver’s workstation and back again. Onward forward motion is triggered by the operator passing a certain point on the vehicle, the so-called “virtual wall”.
If the vehicle is to be loaded from both sides, this can be done using the stop-and-go function. The vehicle moves along in the middle of the aisle at a constant speed and is directed forward by the operator using the remote control, ideally worn on a belt. At the same time, the operator walks back and forth behind the vehicle between rack edges to pick up or place goods – a mode of operation that is more likely to be used in smaller warehouses. Here, too, the advantage is that there is no need for the operator to walk back to the vehicle, nor repeatedly climb on and off it.
Both functions are based on ultra-wideband radio technology and can be set with centimeter precision. At the end of the aisle, the truck stops automatically to avoid collisions with other vehicles. By getting onto the truck, the employee ends the semi-automatic mode and can direct the vehicle manually to the next aisle.
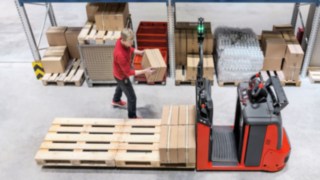
One of the most common processes that take place in high rack warehouses is that of picking on one side of the rack, during which an employee walks along the aisle and back. This activity is supported by the accompanying vehicle’s semi-automatic “follow-me” function.
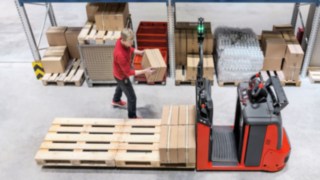
One of the most common processes that take place in high rack warehouses is that of picking on one side of the rack, during which an employee walks along the aisle and back. This activity is supported by the accompanying vehicle’s semi-automatic “follow-me” function.
Safety on board
Since one of the biggest concerns about automated vehicles is the issue of safety, Linde Material Handling has equipped its N20 SA and N20 C SA order pickers with a high-performance safety scanner that is able to detect people and other industrial trucks in the surrounding area. Mounted very low on the chassis, the scanner can also spot unexpected obstacles and is therefore able to prevent collisions and accidents. To avoid damage to racks and give operators enough leeway to do their job, the vehicle maintains a minimum distance of 50 centimeters from the racks but can also be positioned at a greater distance at the beginning of the aisle, if desired.
Measurable advantages
Semi-automatic order picking has already been extensively examined: Linde’s own tests, based on work cycles borrowed from real operations, have shown that performance can be increased by up to 20 percent compared to manual picking. “The new vehicle option usually pays for itself within a short time thanks to shorter routes, greater operating convenience and thus enhanced picking performance, as well as the prevention of costly errors,” reports Philipp Stephan.