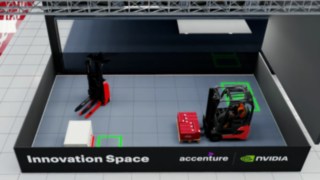
AI for real-time control of industrial trucks
10 Mar 2025
Linde Material Handling showcase demonstrates how artificial intelligence is revolutionizing intralogistics
In the future, warehouse managers will increasingly be able to rely on artificial intelligence (AI) when it comes to optimizing material flow processes. At its tech showcase at the LogiMAT trade fair in Stuttgart, Linde Material Handling (MH) will demonstrate how this product vision works and is gradually becoming reality. The solution is based on NVIDIA’s powerful Omniverse AI platform, which uses a digital twin to collect, process and analyze vast amounts of data from warehouse operations in real time. This initiative aligns with Linde MH’s parent company, the KION Group, which recently announced a large-scale collaboration with NVIDIA, a leader in AI, and Accenture, an expert in digitalization, to take industrial automation to a new level.
In an area adjacent to Linde MH’s exhibition stand, a scenario will be staged that could be typical of the warehouse of the future – manual and automated industrial trucks working side by side in perfect harmony with the help of innovative AI technology. This development will be particularly advantageous for operators of large fleets. The integration of intelligent hardware and software, combined with substantial computing power, will guarantee transparency of every process within the warehouse, ensuring more efficient, reliable and flexible order processing through continuous simulation. “Machine learning and neural networks will enhance warehouse efficiency. Throughput will increase, both manual and automated fleets can be optimized and staff can be deployed more efficiently. This will lead to significant cost savings for companies,” says Ulrike Just, Member of the Management Board responsible for Linde MH Sales & Service EMEA. “As a technology and innovation leader in our industry, we are at the forefront of developing AI-based solutions. These solutions represent a significant breakthrough, aiming to enhance our customers’ competitiveness and ensure the long-term efficiency of their material flows. We are planning initial pilot projects with major customers, for whom the return on the investments involved will be particularly high.”
Real-time localization creates transparency
The first step in Linde MH’s strategy is to network manual industrial trucks. To this end, the intralogistics specialist is currently developing a real-time localization system that works both inside and outside the warehouse. It enables seamless tracking of each vehicle’s location using innovative, low-infrastructure ultra-wideband technology. An intelligent display provides drivers with navigation instructions and new or updated transport orders, with the system combining location data with vehicle data such as the steering angle. This allows routes to be adjusted in real time if, for example, there is too much traffic on a route, causing delays.
At some point, AI becomes indispensable
As warehouse operations become more complex, the optimization of routes and coordination of manual and automated industrial trucks places much higher demands on computing power. “When there are 100 or more vehicles to coordinate, it’s essential to utilize higher-level intelligence and hardware capable of handling such extensive data volumes,” explains Ron Winkler, Managing Director of the Digital Business Unit at Linde MH. “This is where the NVIDIA Omniverse platform’s AI comes in. It creates a digital twin of the warehouse, a virtual 1:1 replica of the physical environment.” In this digital twin, simulations can be run in fractions of a second – either to optimize routes and optimally coordinate AMRs and manual forklifts, or to achieve optimizations in existing warehouse layouts.
The key advantage is that solutions to changing warehouse conditions, such as new orders or inventory fluctuations, traffic congestion in certain warehouse areas, obstacles or overhanging loads, can be identified in real time, simulated in the digital twin and communicated back to the vehicle control system. For instance, if a truck arrives late, the system can automatically assign the nearest forklift equipped for unloading. To achieve this, the NVIDIA Omniverse platform digitally stores all physical data on industrial trucks (e.g., engine power, steering angle) and infrastructure (e.g., rack locations, routes, machine times). This virtual space then processes the constant stream of information coming from sensors, intelligent vehicle and infrastructure cameras, warehouse management software and vehicle control systems.
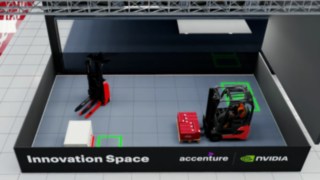
With a tech showcase at the LogiMAT trade fair, Linde MH is showing how artificial intelligence is taking intralogistics to a new level.
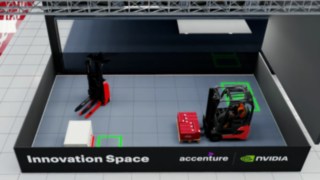
With a tech showcase at the LogiMAT trade fair, Linde MH is showing how artificial intelligence is taking intralogistics to a new level.
Simulation is the key
Intelligent camera systems, strategically installed throughout the warehouse infrastructure and on both manual and automated vehicles are used to track load carriers, AMRs and manual vehicles. They also provide real-time monitoring of loading and storage areas. The images captured by these systems are then interpreted and processed directly by the AI.
The showcase at Linde’s stand will demonstrate this in practice: A forklift driver transports goods to the receiving area using a Linde electric forklift. In the designated transfer area, a fully automated Linde pallet stacker then picks up the pallet for further transport into the warehouse. To seamlessly document and track materials and goods on the Omniverse platform, the manual truck’s mobile, intelligent camera automatically takes a picture of the load when the pallet is picked up and stores it in the system. Concurrently, the camera captures the entire environment, identifying people and obstacles and instantly adapting the vehicle’s behavior to the situation. The stationary cameras in the warehouse provide the system with information about the occupancy of the storage locations, while also detecting potential collisions with people, which would cause the trucks to reduce speed.
However, what if the forklift driver does not place the pallet precisely on the specified surface, as an AGV typically requires? Via the stationary cameras, the digital twin recognizes the pallet’s placement and directs the picking order to the Linde L-MATIC core. Thanks to the intelligent camera on the fully automated AGV, the AI detects the tilted pallet and determines a solution – in this case, the best approach to picking up the load. The cameras also identify problems such as cartons slipping or part of the load overhanging. In such cases, the AI concludes that the AGV should not pick up the load. The Linde L-MATIC core would halt and be reassigned to another transport order. Meanwhile, the AI calculates which manual guided vehicle is nearby to take over the transport task.
“By configuring a digital warehouse twin, any conceivable infrastructure and fleet configuration can be simulated in 3D and tested for efficiency,” explains Ron Winkler. “The AI can be continuously trained and refined. This sets the stage for a warehouse ecosystem that proactively solves challenges and keeps getting better and better.”